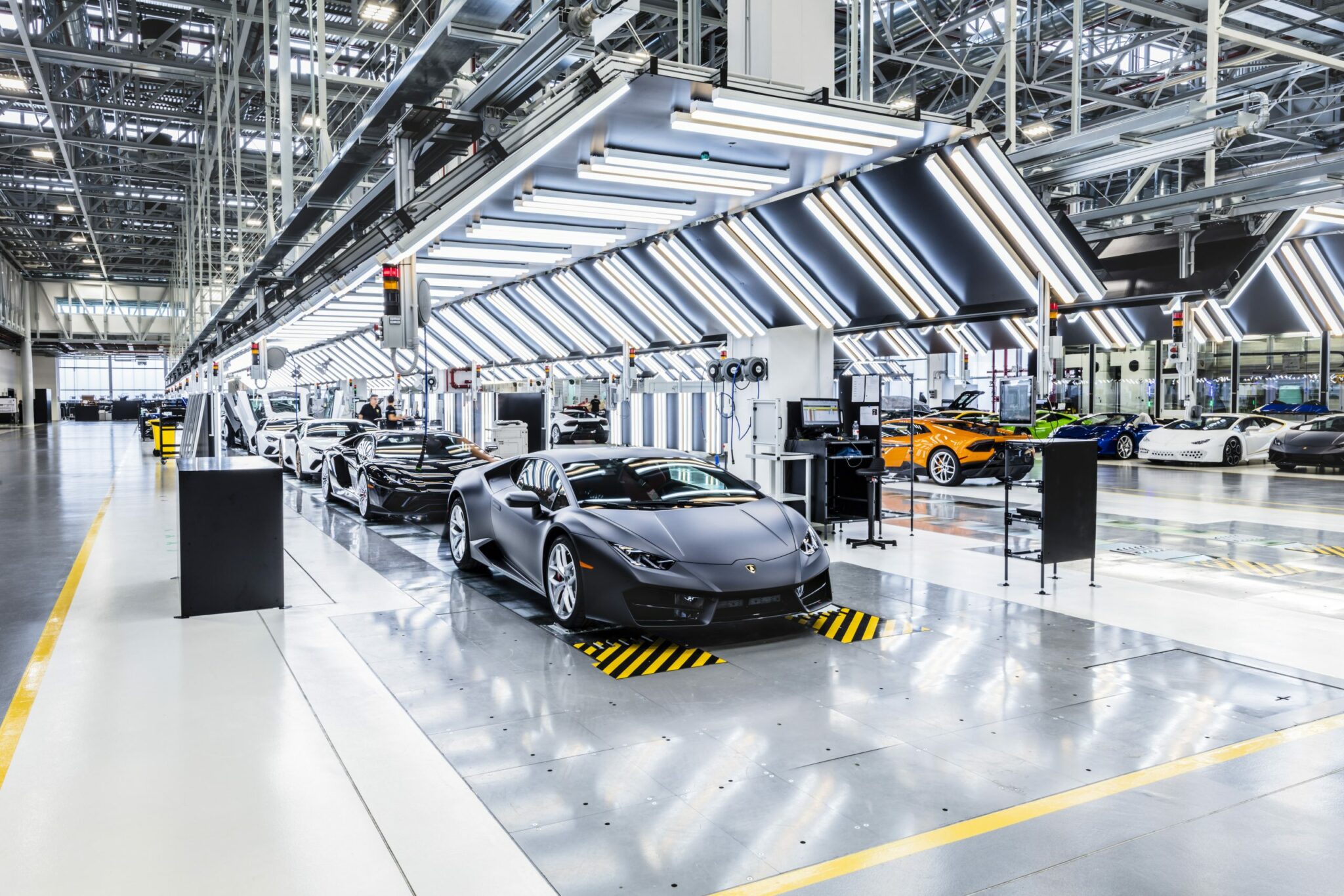
In The Past, The Automotive Industry Has Relied Heavily On Traditional Techniques That Involve Significant Upfront Tooling And Setting Up Production Lines, Lengthy Lead Times, And Expensive Equipment And Design Investments. Additive Manufacturing Can Help With It.
As Long As Automobile Manufacturing Companies Continue To Use And Emerge 3D Printing In Manufacturing And Production, They Will Continue To Gain Advantages In This Sector.
Here We Have Listed Five Companies That Demonstrate The Beneficial Impact That 3D Printing Has Had On The Automotive Sector:
Development Of Prototypes Using 3D Printing At Skorpion Engineering
Skorpion Engineering Is A Leading Innovator In Cutting-edge Car Prototypes. In Order To Generate High-performance Prototypes And Employ Creative Prototyping To Get Conceptual Designs Onto The Market Swiftly And Maintain Their Competitiveness, They Make Use Of Stratasys PolyJet And FDM 3D Printers.
Traditionally, Structural Components Like Bumpers Are Frequently Produced Using Speciality Materials Like Clay Through Outsourcing. Clay Components Are Fragile, Therefore Handling Them While In Transit Is Dangerous. Since Such Material Is Delicate, A Specific Provider Is Usually Needed.
Such Components Can Be Expensive And Time-consuming To Outsource. Making Changes To The Original Design Simply Makes The Production Process More Time- And Money-consuming.
When Skorpion Engineering 3D Printed The 1.4 M / 4.6 Ft Bumper, They Showed How Manufacture Of Such Parts May Be Accelerated.
Stratasys Application Engineers Partnering On High-Performance Parts
Engineers Set Out To Cool The Interior Of NASCAR's Next-Gen Car, Meet Temperature And Durability Criteria And Maintain A Competitive Cost-per-part For Quantities To Address The Severe Heat Temperatures Seen Within Vehicle Cockpits. One Significant Restriction Applied: The Next Gen Car's Design Could Not Be Altered. One Significant Restriction Applied: The Next Gen Car's Design Could Not Be Altered.
Using SAFTM Technology On The H350TM Printer And Assistance From Stratasys Application Engineers, The Team Devised A Method To Meet This Criteria.
After Testing A Number Of Solutions, Stratasys Direct Manufacturing Engineers Suggested That NASCAR Employ SAFTM Technology, Which Is Fueled By The Stratasys H350TM 3D Printer. They Devised A Revised Ventilation Design That Called For The Printing Of More Than 650 New Air Ducts And Ventilation Components Along With The Application Of Many Complex Production Techniques.
The H350 Was Used For Printing, Followed By The DyeMansion Powershot C For Blasting The Pieces Clean, The DyeMansion DM60 For Dyeing Them Black, And The Powershot S For Shot Peening.
The Next Gen Car Was Able To Compete In The 2022 NASCAR Cup Racing Season Because To The Parts' Prompt Completion.
Volvo Revolutionizing Prototyping To Saves Time And Money
A New Water Pump Housing Was Created By Heavy Construction Vehicle Manufacturer Volvo Construction Equipment (VCE) For Use In One Of Their Articulated Transporter Vehicles. In Order To Validate The New Design And Conduct Functional Testing, They Needed A Prototype. Such A Tooling Prototype Would Have Been Significantly Expensive And Prohibitive .
To Build Water Pump Housing Prototypes For Functional Testing, They Used 3D Printing. An Objet Eden260VTM 3D Printer From Stratasys Was Used To Create The Prototype Parts.
Consequently, The Prototype May Be Printed For A Fraction Of The Price Of Typical Prototype Parts. Also They Could Able To Complete Testing Far Sooner And Better Than They Could Have With Traditional Testing Techniques.
Radford Motors Revolutionizes Luxury Car Production
One Of Radford Motors' First Run Vehicles, The Radford Lotus Type 62-2, Was To Be Produced In Just 62 Units, According To The Prototype. Conventional Mass-production Car Manufacture Proved Unfeasible And Prohibitively Expensive.
To Make It Done, They Utilized 3D Printing.
The F770TM And F900^ Types Of Large-format Printers Were Specifically Utilised, With Build Volumes Of 13 And 18 Cubic Feet, Or About Twice The Capacity Of A Bathtub, Respectively. The Thermoplastic Feedstocks Provided The Correct Strength-to-weight Characteristics Required For Producing Tooling And Manufacturing Parts.
With The Printing Capability, They Were Able To Design, Iterate, And Produce The Tooling And Components For Each Bespoke Car Faster And More Affordably Than With Any Other Approach By Using Sturdy, Lightweight Materials.
Lamborghini Leverages 3D Printing For Enhanced Design And Manufacturing
From Direct Digital Manufacturing Of End-use Parts To Fast Prototype Applications, The Italian Automaker Lamborghini Employs 3D Printing To Stay Up To Date With The Whole Lifecycle Of Its Parts.
They Employ High-strength End Pieces Made With Stratasys FDM-based 3D Printing Technology, Which Are Robust Enough For High-speed Racing. With The Help Of The Stratasys Fortus 3D Production Systems, Intricate Geometries May Be Produced Quickly.
They Used A Combination Of Technologies, Including A Stratasys Dimension 1200es 3D Printer, A Stratasys Fortus 360mc Production System, And A Fortus 400mc Production System, To Fabricate And Produce Prototype Parts. Examples Of These Pieces Include Section Bumpers, Grills, Attractive Frames, And Engine Compartment Parts.
Along With Aerodynamic Elements Like Conveyors And Air Heaters, They Also Employed The Mix Of Technology To Create A Variety Of Interior Parts, Including Door Panels, Seat Covers, And Steering Wheels.
Not Only Can 3D Printing Save A Lot Of Money And Time For Lamborghini, But It Also Improves Workflow Efficiency Significantly.
Leave your thought here
Your comments are valuable for us. Required fields are marked *