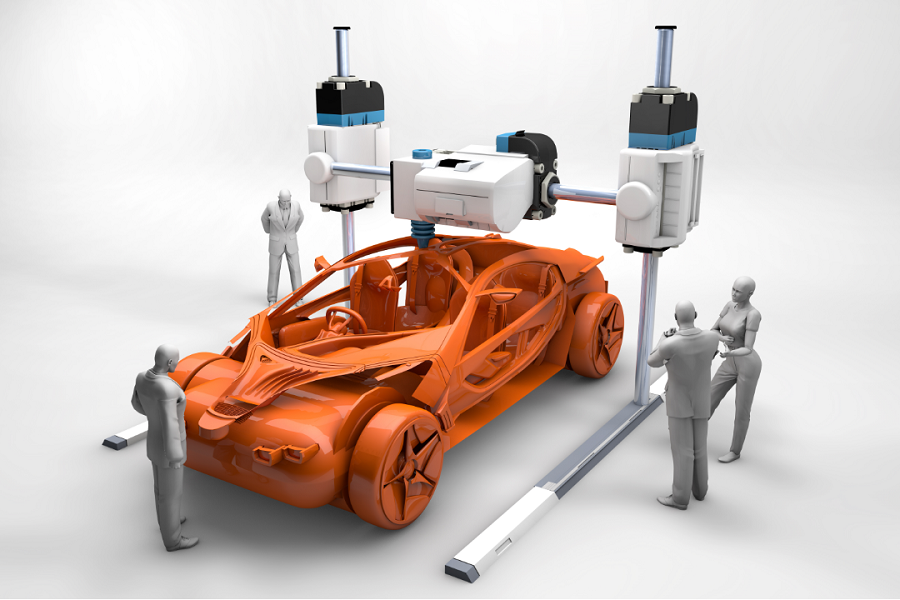
Currently, You Probably Won’t Find A Car That Is Completely Manufactured Using 3D Printing. However, It Is Unlikely That Any Company Has Completely Manufactured A Car Using 3D Printing Processes. There Are A Few Niche Vehicles That Specialize In Using These Methods. Though It Is Still Uncommon, 3D Printing Technology Is Used In Some Cases. In This Blog, We Highlight The Top Automotive Manufacturers In America That Are Widely Using 3D Printing.
Ford
The First In Our List And Biggest Promoter Of 3D Printing In Automotive Manufacturer In USA Is Ford. It’s Headquarter Is In Dearborn, Michigan. This Company Has Been A Champion Of 3D Printing In The Automotive World Since The 1980s, Making It An Early Adopter Of This Transformative Technology.
Ford Has Been At The Forefront With The Stratasys Infinite Build 3D Printing System And Several Cutting-edge 3D Manufacturing Techniques. The Ford Research And Innovation Centre In Metro Detroit Has Been Using This Technology More Frequently, With One Of The Main Reasons To Make Vehicles Lighter. Often, Components Generated Using Additive Manufacturing Weigh Less Than Those Made Using Traditional Methods Because Of Their Special Structural Qualities. Better Fuel Efficiency Is The Result, And This Problem Affects Markets Not Just In North America But Also Internationally. Ford Experts Have Discovered That A Printed Part Can Weigh Up To Half As Much As A Conventional Component In Certain Situations.
Ford Has Had Some Success With 3D Printing In Other Contexts. For Instance, Printing Low-volume Car Parts Is Less Expensive Than Using More Conventional Techniques. When It Comes To Certain Ford Performance Parts, Which Are Only Utilized On Vehicles Like The Explorer ST, This Is Becoming A More Widespread Practice.
Concept Cars And Prototypes Are Excellent Fit For 3D Printing Parts. Ford Engineers Will Occasionally Decide To Print Customised Components Because It Is Notably Faster And Much Less Expensive, Depending On The Precise Parts Being Used.
BMW
BMW, A Renowned German Automaker, Is Among The Best Automobile Brands For 3D Printing. The BMW I8 Roadster Features A Number Of 3D Printed Elements.
The Various Parts Of The Folding Hardtop Should Typically Weigh A Significant Amount. This Not Only Undermines The Car's Touted Fuel Economy, But It Also Causes Handling To Degrade And Rollover Risk To Skyrocket Due To A Substantial Shift In The Centre Of Gravity Of The Vehicle. BMW Reduced Total Extra Weight And Maintained The I8 Roadster's Snappy, Agile Handling By Utilising Printed Elements For The Top System.
BMW Takes Additive Manufacturing Very Seriously. Last Year, It Was Disclosed That A State-of-the-art Autonomous Driving Campus And A New Additive Manufacturing Campus Are Being Constructed In Oberschleissheim. The New Facility Will Cost 10 Million Euros To Construct.
Mini, A Brand Owned By BMW, Has Also Had Remarkable Success With 3D Printed Parts. The British Automaker Has Always Showcased How Customizable Its Cars Are, Appealing To Those Who Wish To Drive Something Special.
The Mini Yours Customised Programme Was Developed Last Year In An Effort To Further Emphasize This Point. It Enables Mini Owners To Buy Certain Parts, Such As Door Sill Plate Or Lamp Cover, With A Fully Unique Design, Phrase, Or Even Their Name Integrated On It.
Usually, Only Extremely Costly Cars Like A Rolls-Royce Phantom Are Eligible For Such A Program. Because Of The Advances In Additive Manufacturing, Mini Can Provide Customers With Personalized Parts At A Reasonable Cost And Get Them Into The Hands Of Car Owners Sooner.
General Motors
One Of The Largest Consumers (as Well As Creators) Of 3D Printing Technology Is General Motors And Its Many Subsidiaries. By 2018, GM Was Saving $300,000 Annually On Tooling And Was Progressing Far Enough In The Creation Of New Technologies Powered By Alternative Fuels. The Top Manufacturer Introduced 20 New Fuel Cell And Electric Vehicle Models Worldwide In 2023.
Despite The Fact That Their 3D Printing Business Has Mostly Focused On Prototype, They Are Growing. As Technology Advances, The Corporation Intends To Increase Printing Capacity To Produce “tens Of Thousands Of Parts At Scale,” As Stated By Kevin Quinn, GM's Head Of Additive Design And Production. I Think This Strategy Will Come To Pass In The Next Five Years.
Every Year, The Company's Warren Tech Centre Produces Over 30,000 Prototype Parts. The Components Use Mixtures Of Polymers, Metal, And Powders To Create At Least Nine Different Types Of Materials. The Company Is Looking At End-use Parts, But Its Primary Use Is Prototyping. Additionally, It Co-owns HRL Laboratories With Boeing, Which Ultimately Produced An Aluminium Alloy That Was 3D Printed.
According To Dan Grieshaber, Director Of GM's Worldwide Manufacturing Integration, Most GM Factories Now Have 3D Printers. The Company Intends To Increase The Number Even More, At Least In Its Plants In North America. The Action Will Probably Save GM Millions Of Dollars A Year In Production Expenses. GM Has A History Of Investing In 3D Printing And Related Technologies.
They Are Using It To Quickly Construct Tools And Accessories For Their Plant Employees. The Company Stated That Just This Year, It Saved $300,000 Over The Course Of Two Years By Implementing A $35,000 3D Printer. Although The Printer's Main Function Is To Produce Tools, It's Feasible That Additive Manufacturing May Become More Important To The Business's Day-to-day Operations
Their Collaboration With Autodesk Has Been Advantageous In Producing Lightweight 3D Printed Components That May Aid The Carmaker In Achieving Its Objectives Of Expanding Its Range Of Products To Include Alternative-fuel Vehicles. Also Part Of This Same Partnership, In 2019 Both Companies Present 3D-printed Seat Bracket Made Of Stainless Steel That Developed Under Autodesk Technology.
Volvo: Embracing 3D Printing For Prototyping And Beyond
While Volvo Not Being The Most Popular Manufacturer Using Automotive 3D Printing, But It Has Made Significant Progress In This Area Recently. Like Other Automotive Manufacturers, Volvo, Has Been Using 3D Printing For Managing Its Supply Chain And For Making Tools. Thanks In Large Part To The Use Of 3D Printing, The Company's Machines Now Have Fresh Prints For Out-of-production Parts. Volvo Now Uses Plastic Pieces That Are 3D Printed, But It Plans To Soon Start Employing Metal Parts As Well.
In 2018, The Company Mostly Used Additive Manufacturing For Tooling And Prototyping. "Prototyping Requires Only Small Quantities Of Parts To Be Produced, So It's A Good Way To See What Works," Says Fredrick Andersson, Development Engineer At Volvo CE (construction Equipment) For Wheel Loaders And Powertrain Installation. "With 3D Printing, We Can Rapidly And Easily Make Adjustments Because We Have A Lot Of Information. It Also Implies That A New Product Can Hit The Market Faster, Which Is Very Advantageous For Our Business.
The Increased Speed Of Prototyping Has Greatly Fasten Prototyping Process, Proved By The New Technologies They Have Been Testing. For Example, Volvo's Engineers Created Brand-new Water Pump Housings For The A25G And A30G Cars. The Internal Flow Pathways In The Housing Were Designed As Best They Could Using Simulations; Nonetheless, In Order To Confirm The New Design, Functional Testing On A Prototype Was Required. For This Job, The Tooling Would Have Cost About $9,090, And The Part Would Have Cost About $909. The Prototype Would Have Required A Minimum Lead Time Of Twenty Weeks To Produce. However, The Prototype Was 3D Printed In Just Two Weeks For A Cost Of $770.
However, In 2019 The The Business Stepped Up Its AM Processes, Especially With Its Volvo Trucks Division. In 2021, The Manufacturing Community Saw A Lot Of Coverage On Their New River Valley (NRV) Plant In Dublin, Virginia. They've Experimented With Various AM Techniques But Mostly Employ SLS. Using 3D Printing, This Facility Creates More Than 500 Manufacturing Tools And Fixtures That Are Used On The Shop Floor. Major Hub For Automotive Engineering In North America Is Also Located At This Location.
The Company Creates Construction Equipment In Addition To Commercial Vehicles. Indeed, This Facet Of The Business's Operations Has Also Been Impacted By 3D Printing. Volvo Used 3D Printing To Retool Its Articulated Haul Trucks, Which Resulted In A Tenfold Reduction In Prototyping Costs. Thanks To This, They Were Also Able To Reduce The Duration From 20 To Merely 2 Weeks.
Leave your thought here
Your comments are valuable for us. Required fields are marked *